Dlaczego stale chromowo niklowe odporne na korozję korodują w środowiskach wodnych oraz profilaktyka antykorozyjna
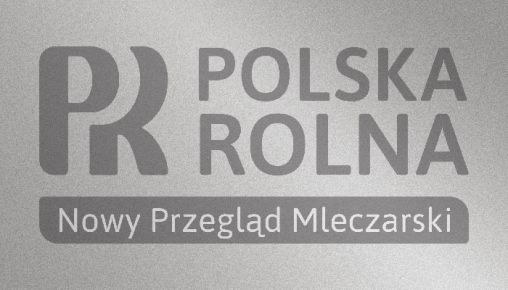
Mgr inż. Jan Marjanowski
Przedsiębiorstwo MARCOR w Gdańsku
Wprowadzenie
Niniejszy artykuł powstał w wyniku serii przypadków korozji stali odpornych na korozję w ostatnim roku. Stale te, zwyczajowo zwane nierdzewnymi, są używane masowo w przemyśle spożywczym oraz w ciepłownictwie. Celem artykułu jest omówienie przyczyn korozji i podanie wytycznych co do sposobów zapobiegania korozji.
Stal austenityczna chromowo niklowa 18-8, oficjalnie zwana stalą odporną na korozję, a w przemyśle spożywczym potocznie zwana stalą nierdzewną, pomimo nazwy i oczekiwań ulega korozji. W przemyśle mleczarskim czy też browarniczym jest to podstawowy materiał konstrukcyjny linii produkcyjnych. Linie te ze względów sanitarnych są myte instalacjami CIP co kilkanaście godzin. Z powierzchni rur, urządzeń mleczarskich, wymienników ciepła i innych urządzeń technologicznych środki myjące usuwają osady mikrobiologiczne, kamienia mlecznego i kamienia wodnego. Kąpiele mają charakter kwaśny lub alkaliczny o utleniającym charakterze. W wyniku technologii CIP i wskutek zastosowanych chemikaliów uzyskujemy czyste powierzchnie i zawsze spasywowane. Powierzchnie takie nie ulegają korozji, posiadają błyszczący i metaliczny połysk powierzchni właśnie wskutek systematycznej obróbki tej stali w celu pasywacji.
Inaczej zachowują się stale chromowo niklowe w instalacjach wody ciepłowniczej, a także chłodniczej, zarówno w przewodach wykonanych ze stali 18-8, jak i w wymiennikach ciepła służących do podgrzewu ciepłej wody użytkowej (c.w.u.). Z obserwacji, własnych badań oraz posiadanej przez autorów dokumentacji fotograficznej wynika, że stal ta w instalacjach c.w.u., a także c.o., niekiedy koroduje mechanizmem korozji wżerowej, co powoduje szybkie w czasie i przedwczesne zniszczenia korozyjne rur lub wymienników ciepła. Ich wymiana jest kosztowna, powoduje często przestoje technologiczne w produkcji i ekonomicznie jest nieuzasadniona.
Celem niniejszego opracowania jest wyjaśnienie przyczyn korozji tej stali w warunkach przeciętnej eksploatacji w zakładzie mleczarskim jak też wskazanie profilaktyki antykorozyjnej, której przestrzeganie wyeliminuje te groźne dla wymienników zjawiska. Szczególnie jest to ważne obecnie, gdy na naszym rynku pojawiły się duże ilości taniej chińskiej stali 304 L. Wykonane instalacje często korodowały już w okresie 1-3 miesiące i wiązało się to głównie z brakiem odpowiedniej obróbki powierzchni tej stali po wykonaniu prac spawalniczych na instalacji, a przede wszystkim trawienia i pasywacji.
Zjawisko pasywacji stali
Stale nierdzewne chromoniklowe zawdzięczają swoje właściwości przeciwkorozyjne zjawisku pasywacji. Metal albo stop jest uważany za pasywny, jeśli wykazuje on znaczną odporność na korozję w takim środowisku, w którym z termodynamicznego punktu widzenia obserwuje się znaczne obniżenie energii swobodnej związanej z przejściem metalu ze stanu metalicznego w odpowiednie produkty korozji [1]. Zjawisko pasywacji wiąże się z utworzeniem na powierzchni metalu warstewki pasywnej charakteryzującej się właściwościami w sposób zasadniczy utrudniającymi dalszy przebieg procesów korozyjnych.
Warstewki te na stalach nierdzewnych odznaczają się m.in. następującymi cechami [2]:
- grubością w granicach 1÷10 mm,
- bardzo dobrą szczelnością,
- elektronowym mechanizmem przewodzenia prądu,
- tworzeniem się w czasie procesu utleniania,
- odpornością chemiczną, hydrofobowością.
Korozja wżerowa austenitycznych stali nierdzewnych
Warstewki pasywne w środowiskach zawierających jony chlorkowe Cl- ulegają niszczeniu (przebiciu), co inicjuje korozję wżerową stali stopowej. Przebicie następuje wskutek przenikania jonów Cl- w miejscach osłabienia warstewki pasywnej [1, 2]. Takimi słabymi miejscami mogą być mikropory lub uszkodzenia warstewki pasywnej spowodowane niejednorodnością strukturalną metalu, np. wtrąceniami niemetalicznymi (szczególnie siarczkowymi) wydzieleniami wtórnych faz, dyslokacjami, obecnością innych atomów w sieci krystalicznej metalu itp. Obok jonów chlorkowych zdolność niszczenia warstewek pasywnych mają jony Br-, J-, ClO-, S2O32 -. Z reguły literatura podaje w zależności od typu stali ich odporność na chlorki. Dla stali 304 niebezpieczna ilość chlorków w środowisku wodnym w podwyższonej temperaturze wynosi ponad 100 mg/l, jednak autorzy spotkali instalacje ze stali 304 w temperaturze 70°C, w których ilość chlorków wynosiła 70 mg/l przy obecności siarczanów w wodzie 50 mg/l, która została zniszczona w ciągu 1,5 miesiąca wskutek wystąpienia korozji wżerowej na powierzchniach rur i na spawach.
W miejscu przebicia warstewki metal jest w stanie aktywnym i w połączeniu z sąsiadujących obszarem pasywnym tworzy lokalne ogniwo korozyjne o dużej powierzchni katody i małej powierzchni anody, a przez to dużej anodowej gęstości prądu [3]. Prowadzi to do szybkiego wzrostu wżeru korozyjnego.
Na rys. 1 przedstawiono przebieg typowej krzywej anodowej polaryzacji stali stopowej pasywującej się [2]. W środowiskach nie zawierających chlorków (krzywa 1), stan trans- pasywny związany jest głównie z wydzielaniem tlenu. Przy obecności w roztworze jonów chlorkowych (krzywa 2), po osiągnięciu potencjału przebicia (Enp.) następuje gwałtowny wzrost prądu spowodowany powstaniem i rozwojem wżerów. Poniżej potencjału przebicia znajduje się tzw. potencjał krytyczny korozji wżerowej (Ecp).
Jeśli na skutek warunków środowiskowych metal spasywowany posiada potencjał niższy od Ecp, korozja nie zachodzi. Jeśli potencjał powierzchni metalu ma wartość pomiędzy Ecp i Enp. nowe wżery nie powstają, ale już istniejące rozwijają się. Powyżej Enp. następuje inicjacja nowych wżerów.
W procesie korozji wżerowej wyróżnia się dwa stadia:
- inicjacja wżeru trwająca, w zależności od warunków, od kilku minut do kilkunastu miesięcy,
- rozwój wżeru następujący z wzrastającą szybkością aż do perforacji stali lub momentu przerwania procesu wskutek zmiany warunków środowiskowych.
.jpg)
Rys. 1. Wpływ korozji wżerowej na kształt krzywej polaryzacji anodowej spasywowanej stali stopowej [2].
- – przy braku w roztworze jonów chlorkowych
- – w obecności jonów chlorkowych
Inną cechą charakterystyczną korozji wżerowej jest autokatalityczny tzn. samo przyspieszający przebieg rozwoju zainicjowanego wżeru. Rosnący wżer stwarza warunki sprzyjające dalszemu wzrostowi szybkości roztwarzania metalu. Zjawisko to przedstawiono schematycznie na rys. 2.
.jpg)
Rys. 2. Autokatalityczny charakter procesu korozji wżerowej [1].
Powierzchnia wżeru stanowi anodę lokalnego ogniwa korozyjnego i na niej zachodzi reakcja roztwarzania metalu:
Me --> Me2+ + 2e
Na powierzchni metalu, sąsiadującej z wżerem, przebiega reakcja katodowa:
½ O2 + 2H2O + 2e --> 2OH-
Płynący w ogniwie prąd elektryczny powoduje wędrówkę jonów Cl- do wnętrza wżeru i tworzenie stężonego roztworu chlorku metalu. Hydroliza chlorku:
MeCl2 + 2H2O --> Me(OH)2 + 2HCl
wywołuje zakwaszenie roztworu we wżerze i wytrącenie trudno rozpuszczalnego wodorotlenku metalu. Wzrost zakwaszenia wraz ze wzrostem stężenia jonów Cl- zwiększa szybkość roztwarzania metalu, co pociąga za sobą wzrost prądu ogniwa i dalszą wędrówkę jonów Cl- do wnętrza wżeru. Zgodnie z zasadą zachowania ładunku, zwiększeniu szybkości reakcji anodowej (roztwarzania metalu) towarzyszy wzrost szybkości reakcji katodowej (redukcji tlenu) tak, aby wszystkie elektrony uwalniane podczas jonizacji metalu zostały zużyte w reakcji redukcji.
Na przebieg korozji wżerowej może mieć wpływ szereg czynników wewnętrznych (w stopie) i zewnętrznych (w środowisku). Ogólnie im wyższa jest zawartość w stali chromu, niklu i molibdenu oraz im mniejsza jest zawartość węgla, wydzielin węglików, faz wtórnych, wtrąceń mechanicznych – tym mniejsza jest podatność stali na korozję wżerową. Powierzchnia gładka jest trudniej atakowana przez korozję wżerową niż powierzchnia chropowata.
Korozję ułatwiają stałe naprężenia wynikające np. z odkształcenia blachy na skutek tłoczenia) lub zmienne (powstające np. przy pulsującym ciśnieniu) naprężenia rozciągające.
Do czynników zewnętrznych sprzyjających korozji wżerowej stali odpornych na korozję należy zaliczyć:
- obecność jonów halogenowych, szczególnie Cl-,
- obecność utleniaczy (O2, Fe3+, Cu2+, Hg2+, MnO2),
- podwyższona temperatura,
- brak cyrkulacji roztworu (martwe przestrzenie).
Wokół uczulonych punktów, gdzie rozpoczął się proces anodowego roztwarzania, osadzane są m.in. tlenki manganu. Pobierany z wody tlen tworzy wyższe tlenki, stymulujące proces katodowy. Działanie ogniwa aktywno-pasywnego ułatwia fakt, że tlenki manganu charakteryzują się przewodnictwem elektronowym.
Korozja szczelinowa i podosadowa
Mechanizm korozji szczelinowej i podosadowej jest bardzo podobny do mechanizmu korozji wżerowej. Stal nierdzewna austenityczna powinna być nie pokryta żadnymi osadami. Zapewnia to równomierny dopływ tlenu do całej powierzchni stali i jednorodny potencjał elektrochemiczny na powierzchni. W przypadku gdy na powierzchni stali znajduje się osad, który jest luźno związany z powierzchnią i jest on porowaty jak np. tlenki żelaza w instalacji c.o., osady na powierzchni wymiennika c.o. lub c.w.u. dochodzi do powstawania mikroogniw korozyjnych wskutek różnych stężeń tlenu na powierzchni metali. Z reguły tlen pod warstwą osadu ulega zużyciu na odbudowanie się warstewki pasywnej. Natomiast w miejscach niejednolicie pokrytych osadem dopływ tlenu jest ułatwiony. Powstają różne potencjały rzędu 50¸100 mV pomiędzy powierzchnią anodową (pod osadem) a powierzchnią katodową, która stanowi odsłoniętą część powierzchni metalu. Pod osadem niszczony jest stan pasywny wskutek zainicjowanego procesu elektrochemicznego.
Aby wystąpiła korozja stali nierdzewnej niezbędne jest [4]:
- obecność czynnika utleniającego, najczęściej tlenu, tworzonego ogniwo stężeniowe,
- obecność jonów aktywujących – zwykle chlorkowych,
- dostatecznie mała pojemność roztworu buforowego, umożliwiająca powstanie znacznej różnicy pH pomiędzy szczeliną pod osadem a powierzchnią.
Korozja szczelinowa występuje w szczelinach np. pod uszczelkami. Szczelina może się tworzyć w miejscu silnie skręconych płyt wymiennika płytowego, gdzie środowisko jest nieruchome, np. w miejscu styku dwóch płyt.
Korozja podosadowa jest odmianą korozji szczelinowej i wiąże się z obecnością niewielkich ilości nieruchomego elektrolitu w szczelinach i załomach o szerokości od kilku setnych mm do kilku mm, którego nieruchomość wynika z przyczyn osadzania się na powierzchni metalu produktów korozji, piasków oraz porastania biologicznego.
Walka z korozją podosadową sprowadza się albo do utrzymania czystości powierzchni stali nierdzewnej lub też poprzez dodatek inhibitorów korozji do wody, na tyle zwiększony, aby wymusić jednolite działanie inhibitora pod warstwą półprzepuszczalnego porowatego osadu. Badania Politechniki Gdańskiej wykazały, że w temperaturze powyżej 30oC w przypadkach gdy na powierzchni stali 316 L znajduje się szlam, stal ta jest narażona na korozję szczelinową już przy małej zmianie stężenia utleniacza [2].
Należy nadmienić, że powyższe rozważanie nie dotyczy stali pokrywanej warstewką węglanu wapnia CaCO3. Warstewka ta jest szczelna i w sposób zaporowy izoluje metal od środowiska. Zwykle wymienniki ciepła w obiegach podgrzania ciepłej wody użytkowej nie korodują, gdyż po czasie kilku dni pokryte są już cienką warstewką CaCO3, która szczelnie odcina powierzchnię metalu od środowiska. Zdarza się także mieszany skład warstewki osadów, tzn. tworzą ją związki CaCO3 oraz związków żelaza. Taka warstewka zwykle nosi charakter warstewki porowatej i jest przepuszczalna dla składników roztworu wodnego.
Wpływ dodatków stopowych na szybkość korozji stali nierdzewnych
Stale nierdzewne austenityczne 18-8 (ok. 18% Cr i ok. 8% Ni) pod względem składu chemicznego są znormalizowane. W Polsce skład ich określany jest przez polską normę PN, a w krajach Unii Europejskiej oraz w USA przez normatyw American Iron and Steel Institute (AISI).
Stale wytwarzane w Polsce na wymienniki ciepła zgodnie z normą PN-71/H/86020, to stale:
- 1H18N9T,
- 1H18N10MT.
Wg normatywu AISI na wymienniki ciepła przeznacza się głównie stale:
- 304 (wg oznaczeń europejskich 1.4301),
- 316 L (wg oznaczeń europejskich 1.4404).
Stal 304 i 1H18N9T nie zawierają w swoim składzie molibdenu a stal 316 i 1H18N10MT zawiera molibden.
Skład chemiczny stali austenitycznej przedstawiono poniżej w tabeli 1.
Tab. 1. Skład chemiczny stali nierdzewnych wg PN-71/H-86020 oraz AISI
Lp. |
Składniki chemiczne stali |
1H18N9T % |
1H18N1OMT % |
304 (AISI) % |
316 (AISI) % |
1. |
C(max) |
0,10 |
0,10 |
0,08 |
0,08 |
2. |
Cr |
17,0¸19,0 |
17,0¸20,0 |
18,0¸20,0 |
16,0¸18,0 |
3. |
Ni |
8,0¸10,0 |
9,0¸11,0 |
8,0¸10,5 |
10,0¸14,0 |
4. |
Mn (max) |
2,0 |
2,0 |
2,0 |
2,0 |
5. |
P (max” |
- |
- |
0,045 |
0,045 |
6. |
S (max) |
- |
- |
0,03 |
0,03 |
7. |
Si (max) |
0,8 |
- |
1,0 |
1,0 |
8. |
Ti (max) |
5 x C – 0,8 |
5 x C – 0,8 |
Nie norm. |
5 x C |
9. |
Mo |
- |
1,5¸2,2 |
- |
2,0¸3,0 |
Dodatek tytanu do stali 18-8 powoduje możliwość zwiększenia ilości węgla w stali, przez co zmniejsza on korozję międzykrystaliczną spowodowaną przez węgliki chromu na granicy wżeru austenitu. Molibden w stalach austenitycznych uodparnia je przed korozją spowodowaną przez chlorki, a więc przed korozją wżerową i szczelinową.
- ływ utleniaczy, odczynu pH i inhibitorów korozji na korozję stali austenitycznych w środowiskach wodnych
Jak już wcześniej zaznaczono w pkt. 3, ogólnie utleniacze typu jonów Fe3+ i Cu+2 oraz MnO2 i O2 przyspieszają korozję wżerową stali nierdzewnej jeśli ich stężenie jest niedostateczne, szczególnie tam, gdzie występuje podwyższona temperatura roztworu, brak cyrkulacji na powierzchni i są obecne jony chlorkowe.
Przeciwnie: obniżenie temperatury powierzchni stali, obecność reduktorów oraz wyeliminowanie z wody jonów Fe+3, Cu+2 oraz związków manganu Mn+2, który łatwo się utlenia do MnO2 prowadzi do podwyższenia odporności tej stali w wodach. Nie bez znaczenia jest pH roztworu, przy pH powyżej 9 korozja wżerowa rzadziej występuje niż przy pH około 7, ze względu na chociażby przerwanie się ciągu reakcji autokatalitycznego zakwaszania się przestrzeni wewnątrz powstającego wżeru (patrz pkt. 3).
Niektóre aniony i związki chemiczne mają zdolność hamowania korozji wżerowej nawet w roztworach zawierających znaczne ilości chlorków. Hamujące działanie wykazują jony: OH-, NO3-, SO4-2, SiO3-2, ClO4 – o ile znajdują się w roztworze w dostatecznym stężeniu. W pracy zbiorowej [3] „Technika przeciwkorozyjna” cz. II, autorzy wyraźnie wskazują, że aby ustrzec się korozji w układach wodnych, w których występują wymienniki ciepła i może występować korozja szczelinowa (podosadowa) powinny być dodawane zwiększone dawki inhibitorów korozji aby zapewnić dostateczne i równomierne stężenia inhibitora w miejscach trudno dostępnych.
Niektóre substancje ułatwiają pośrednio pasywację żelaza i stali stwarzając warunki ułatwiające adsorpcję ich na metalu, który jest właściwym pasywatorem. Do tej kategorii należą związki alkaliczne NaOH, Na3PO4, Na2B4O7. Wszystkie te związki są substancjami nieutleniającymi i w związku z tym tlen rozpuszczony w wodzie słusznie jest również uważany za substancją pasywującą. Z doświadczeń MARCOR w kooperacji z firmami duńskimi wynika, że dodatek do wody w instalacji c.o. związków organicznych typu tanina, które mogą wytwarzać jednocześnie warstewki ochronne taninianów żelaza eliminuje korozję stali nierdzewnych typu 18-8 w wymiennikach ciepła z blach ze stali nierdzewnej. Jest to prawdopodobnie spowodowane przesunięciem krzywej polaryzacji katodowej na zakres poza pasywny, w którym nie występuje tendencja do korozji wżerowej stali 18-8. Powyższe zilustrowano na Rys. 3 [3].
.jpg)
Rys. 3. Wpływ stężenia inhibitorów utleniających na korozję układu pasywującego [3]
A – krzywa przebiegu procesu anodowego
K1 – K4 – krzywa przebiegu reakcji katodowych przy różnych stężeniach (C1¸C4) pasywatora
Jak widać z powyższego rysunku, niedostateczne stężenie czynnika pasywacyjnego może być przyczyną wzrostu szybkości korozji z uczuleniem stali na korozję wżerową. W tym przypadku lepszy może być dodatek inhibitora o własnościach redukcyjnych, gdyż w tym zakresie szybkość korozji stali 18-8 jest niska, a nie występuje obszar potencjałów, w którym stal jest uczulona na korozję wżerową (poniżej zakresu potencjału Ecp).
Korozja naprężeniowa stali nierdzewnych
Stale typu 304 ( 1.4301) i 316L (1.4404) mogą ulegać zjawiskom korozji w wyniku korozji naprężeniowej związanej z jednoczesnym występowaniem naprężeń (wynikających z konstrukcji elementu, jego obróbki, spawania, itd.), wysokiej temperatury (50-60°C) i jonów chlorkowych. W takim przypadku zapobieganie korozji polega na wyeliminowaniu jednego bądź wszystkich czynników niezbędnych do wystąpienia korozji naprężeniowej.
W praktyce przemysłowej zaobserwowano naprężeniowe pękanie korozyjne austenitycznych stali nierdzewnych w rurach gorącej wody ze stali nierdzewnej. W takiej sytuacji można wyeliminować np. chlorki występujące w użytkowanej wodzie przez zastosowanie procesu wymiany jonowej – demineralizacji (usuwanie z wody chlorków i siarczków), co przy właściwej kontroli i monitorowaniu instalacji może być skutecznym rozwiązaniem.
Korozja naprężeniowa ma miejsce, gdy nastąpi pękniecie ochronnej warstwy pasywnej i wskutek działań naprężających nie odnowi się warstwa pasywna.
Obraz korozji naprężeniowej na materiale przedstawiony jest jak korzeń rośliny co pokazano na rysunku 4.
![]() |
Rys. 4 Charakterystyczny obraz korozji naprężeniowej
(źródło:http://www.im.mif.pg.gda.pl/download/materialy_dydaktyczne/PIM_18_stale_odporne_na_korozje.pdf)
Korozja międzykrystaliczna, przyspoinowa i nożowa stali nierdzewnych austenitycznych
Austenityczne stale odporne na korozję stają się podatne na korozję międzykrystaliczną podczas wygrzewania w temperaturze 400-850°C wskutek wydzielania się węglików chromu zamiast węglików tytanu. Pełen zakres zmian w stali związanych ze zmianą z temperaturą pokazano w tabeli 2.
Tab. 2. Przebieg reakcji w stali chromowo niklowej z dodatkiem tytanu w zależności od temperatury [ 3 ]
Zakres temperatury w °C |
Reakcje |
< 400 |
Nie zachodzą |
400-500 |
Wydzielanie węglików chromu |
850-1260 |
Rozpuszczanie węglików chromu, wydzielanie węglików tytanu |
1260 – do T topnienia |
Rozpuszczanie węglików chromu, wydzielanie węglików tytanu |
Korozja międzykrystaliczna stali austenitycznych jest wynikiem zubożenia przygranicznych strefy podgrzania obszarów ziaren austenitu w chrom czyli tzw. dechromizacji. Na granicy ziarna wytraca się węglik chromu, a ziarno ubożeje w chrom. Dla utrzymania stanu pasywnego stali konieczna jest zawartość chromu w ilości co najmniej 12%, a bywa tak że stężenie chromu spada do kilku procent, a nawet do zera. Jeżeli stal nagrzaną do temperatury ponad 1000°C ochłodzić bardzo szybko, np. przez zanurzenie w wodzie, to nie zostanie ona uczulona na korozję międzykrystaliczną. Czas przebywania stali w zakresie temperatury 400-850°C będzie zbyt krótki, aby węgiel mógł przedyfundować do granic ziaren i przereagować z chromem.
Stal austenityczna po podgrzaniu szczególnie powyżej 650°C ulega korozji w zetknięciu z środowiskami korozyjnymi i zaczyna korodować wzdłuż granic ziaren austenitu. Dlatego strefy przyspoinowe ulegają szczególnej korozji co pokazano na rysunku 5 [3].
![]() |
Rys. 5. Korozja przyspoinowa stali austenitycznej chromoniklowej 18/8.
Korozja nożowa jest szczególnym typem korozji międzykrystalicznej. Niszczenie następuje w wąskiej strefie metalu bezpośrednio przylegającej do spoiny pozostawiając ślad podobny do cięcia nożem, stąd nazwa tego rodzaju korozji.
Korozji międzykrystalicznej można zapobiec o ile podda się materiał spawany normalizacji w temperaturze 1100°C celem wygrzania materiału. Niestety nie da się wygrzać dużych instalacji, a jedynie elementy.
Korozyjność wody w stosunku do stali nierdzewnych
W Polsce normą pozwalającą na dokonanie oceny ryzyka korozyjności wody w stosunku do stali odpornych na korozję jest norma PN-EN 12502 -4. Norma ta odnosi się do systemów rozprowadzania i magazynowania wody o jakości jak dla ludności.
Zgodnie z tą normą do oceny wpływu własności wody wymagane są dane dotyczące własności wody wg cz. 1 tej normy (PN-EN 12502 -1), w szczególności zawartości Cl-, wartość pH, jak również rodzaj i stężenie substancji utleniających np. stosowanych do dezynfekcji. W normie tej stwierdza się, że korozja wżerowa występuje w wodach, które zawierają Cl- w ilości powyżej 6 mmola/l.
Występujące w wodzie inne aniony (np. azotany, fosforany, krzemiany, węglany) mogą działać inhibitująco na korozję wżerową lub są bez wpływu.
Przy pozostałych warunkach stałych istnieją następujące tendencje:
- wzrost prawdopodobieństwa uszkodzeń poprzez:
- wzrost zawartości jonów Cl-. Przy stosowaniu stali bez zawartości molibdenu stężenie chlorków powinno być niższe od 6 mol/m3 (< 213 mg Cl- /dm3 ),
- wzrost stężenia tlenu lub innych środków utleniających,
- podwyższenie temperatury.
- obniżenie prawdopodobieństwa uszkodzeń poprzez:
- wzrost stężenia jonów SO42-, jak również NO3-,
- dodatek substancji redukujących.
Decydujący wpływ na prawdopodobieństwo uszkodzeń mają warunki pracy, konstrukcja i obróbka.
Prawdopodobieństwo uszkodzeń jest niewielkie dla stali nierdzewnych 18-8, gdy spełnione są niezbędne warunki:
- odporność na korozję międzykrystaliczną poprzez dobór odpowiedniego składu stopu,
- brak przenoszenia ciepła od materiału do wody, gdy tworzone przez to osady ułatwiają wzbogacenie się w jony Cl- strefy wokół wżeru,
- brak stacjonarnych pęcherzy gazowych,
- brak pokryć lub mas uszczelniających, które jony Cl- mogą wprowadzać lub powodować miejscowe wzbogacenie w jony Cl-,
- fachowo wykonane szwy spawalnicze (gazy ochronne, usuwanie topników).
Korozja wżerowa jest uprzywilejowana w wodach stacjonarnych i zanika w wodach szybko płynących. W instalacjach przemysłowych można jednak korozję obniżyć stosując wysokie szybkości przepływu jak również okresowe wibracje. Przy ogrzanych wodach, zanieczyszczenia i pęcherze gazowe, a w ogólności granice trzech faz, podwyższają prawdopodobieństwo korozji wżerowej lub naprężeniowej.
Przy stosowaniu materiałów uszczelniających, które wprowadzają jony Cl- lub powodują miejscowe wzbogacenie w te jony (np. używanie kleju Butapren do przyklejania uszczelki w wymienniku płytowym zamiast firmowego kleju podawanego przez wytwórcę wymiennika lub uszczelek z chlorowcopochodnych syntetycznego kauczuku), istnieje podwyższone prawdopodobieństwo korozji wżerowej lub selektywnej.
Dla materiałów uczulonych korozja międzykrystaliczna może występować nawet w wodach pozbawionych chlorków, a o jej możliwości inicjacji decyduje podwyższona ponad 50oC temperatura wody.
Na rysunku 6 i 7 przedstawiono fotografię z zewnątrz rury ze stali 304 pracującej 4 tygodnie w wodzie o temperaturze 60°C przy zawartości w wodzie chlorków 95 mg/l i siarczanów 122 mg/l.
W omawianym przypadku korozja elementów rur o średnicy 25, 32 i 40 mm wystąpiła już po 1,5-2 miesiącach od czasu wprowadzenia ciepłej wody użytkowej do rur. Należy jednak wskazać, że nie wykonano żadnej obróbki chemicznej rur tak zewnętrznej jak i wewnętrznej przed oddaniem instalacji do użytku.
|
![]() |
Rys. 6 Fotografia wycinka rury ze stali 304 z drobnymi wżerami korozyjnymi o charakterze igieł. |
Rys. 7 Wycinek zespawanej rury ze stali 304 z przebarwieniami i widocznym zaspawanym wżerem (z prawej strony fotografii). |
Zabezpieczenie przed korozją instalacji ze stali nierdzewnych
Aby zabezpieczyć stal nierdzewną przed korozją już po procesie złączenia (spawania instalacji, zbiorników) należy powierzchnię stali i spawy zabezpieczyć poprzez wytrawianie i pasywację.
Wytrawianie to proces usuwania przebarwień pozostałych po spawaniu stali nierdzewnej, tam gdzie została zmniejszona zawartość chromu na powierzchni stali. Wytrawianie odbywa się za pomocą kwasowych kąpieli trawiących bądź miejscowo za pomocą past i żeli. Proces rozpuszczania niezabezpieczonej powierzchni metalu odbywa się przez zanurzenie drobniejszych elementów konstrukcji w roztworze kwasu azotowego i fluorowodorowego, natomiast większych za pomocą past i żeli.
Pasywacja – to proces wytwarzania stałej warstewki tlenkowej na stali nierdzewnej. Na stali powstaje jednorodna warstewka odporna na korozję. Zwykle uzyskuje się ją w kąpielach kwasu azotowego, cytrynowego, lub czasami fosforowego. Wskutek takiego procesu chrom wydobywa się na powierzchnię i warstewka jest jaśniejsza i odporniejsza na korozję.
Na rysunku 8 i 9 przedstawiono fotografię elementów rurowych ze stali 304 (AISI) eksploatowanych w instalacji ciepłej wody użytkowej o temperaturze 60°C w zakładzie spożywczym. Woda posiadała w tej temperaturze przewodnictwo 920 µS/cm oraz zawierała w swoim składzie chemicznym: chlorków 95 mg/l i siarczanów 122 mg/l przy niskiej zasadowości „m” wynoszącej 1,6 mval/l. Pierwsze przecieki zaobserwowano po 1,5 miesiąca od uruchomienia instalacji, po 2,5 miesiącach zdemontowano instalację ze względu na dużą liczbę przecieków.
Praktycznie przecieki w formie miejscowych wżerów znajdowały się na ok. 70% złączy spawanych. Instalacja nie była trawiona i pasywowana po montażu. Natychmiast po montażu i próbie wodnej wpuszczono do niej ciepłą wodę użytkową z wymienników ciepła.
|
![]() |
|||
Rys. 8 Element rurowy ze stali 304 po 2 miesiącach pracy w instalacji ciepłej wody A) – element po wycięciu z instalacji c.w.u. B) – dopełniający element po wycięciu z instalacji, trawieniu i pasywacji. |
Rys. 9 Rura DN 32 ze stali 304 po 2 miesiącach pracy w instalacji ciepłej wody A) – połówka rury po wycięciu z instalacji B) – druga połówka rury po wycięciu z instalacji, trawieniu i pasywacji. |
W ramach eksperymentu wycięte elementy rurowe z instalacji ciepłej wody przecięto wzdłuż, a następnie jeden z elementów zanurzono w roztworze trawiącym do 10% kąpieli preparatu Radiner Fi (produkt MARCOR) w temperaturze 35°C na przeciąg 4 godzin, a następnie do tej samej kąpieli dodano na 1 dm3 kąpieli 1,5 ml 30% roztworu nadtlenku wodoru wytwarzając kąpiel pasywacyjną. Jednocześnie mierzono potencjał elektrochemiczny wycinków rur stosując jako elektrodę odniesienia nasyconą elektrodę siarczano cynkową. Po ok. 2 godzinach od rozpoczęcia procesu pasywacji potencjał elektrochemiczny powierzchni stali 304 wzrósł o 200-220 mV w stosunku do okresu sprzed dodania nadtlenku wodoru.
Gdyby instalator instalacji ciepłej wody użytkowej dokonał trawienia rur i jednocześnie pasywacji, uodpornione rury prawdopodobnie nie uległyby korozji miejscowej, choć być może ze względu na wysoką korozyjność wody zabieg trawienia, zdaniem autora, powinien być powtarzany co 2 lata.
Podsumowanie
- Odporność stali nierdzewnych na korozję jest ograniczona i zależy od czynników:
- materiałowych (składu chemicznego),
- warunków środowiskowych (składu chemicznego otoczenia w którym przebywają),
- temperatury środowiska,
- przepływu hydraulicznego,
- sposobu spawania i gazu ochronnego,
- braku wytrawienia i pasywacji powierzchni po montażu,
- i wielu innych trudnych do zdefiniowania czynników jak np. korozja mikrobiologiczna.
- Stale nierdzewne austenityczne narażone są na korozję:
- wżerową,
- szczelinową i podosadową,
- międzykrystaliczną,
- przyspoinową ( w tym nożową),
- naprężeniową.
O wystąpieniu określonego typu korozji decyduje wiele czynników, niemniej uszkodzona powierzchnia warstwy pasywnej i warunki środowiskowe, w tym głównie chlorki, a także czynniki temperaturowe i brak przygotowania powierzchni stali po montażu, sprzyjają głównie korozji wżerowej, przyspoinowej i naprężeniowej.
- Profilaktyka antykorozyjna dla nierdzewnych austenitycznych stali sprowadza się do:
- wytrawienia i pasywacji powierzchni stali po montażu,
- unikania środowisk z nadmiarowymi jonami chlorków i siarczanów w zależności od wytycznych producenta dla danego typu stali,
- unikaniu wysokich temperatur i bezruchu środowiska.
Literatura:
- H. Uhlig, Korozja i jej zapobieganie, WNT, Warszawa, 1976.
- R. Juchniewicz i inni, Ekspertyza przedsiębiorstwa „COPROLEX” pt. Określenie przyczyn i mechanizmu korozji płyt wymienników ciepła „Vicarb” w Policach, Gdańsk, 1989.
- R. Juchniewicz i inni, Technika przeciwkorozyjna cz. 2, WSziP, Warszawa, 1976.
- G. Wranglen, Podstawy korozji i ochrony metali, WNT, Warszawa, 1975.