Wymiana pokoleniowa na rynku ERP
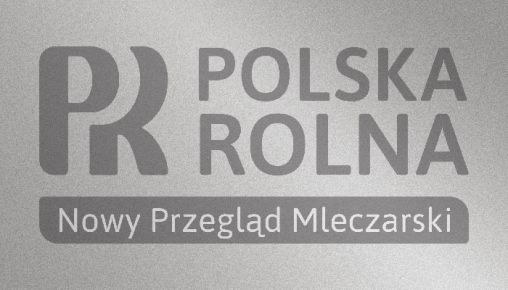
Jak wynika z badań Ventana Research, 45% pytanych przedsiębiorstw chce w najbliższym czasie korzystać z bardziej wydajnych systemów ERP. Podobne nastroje panują na rodzimym rynku. Coraz więcej firm posiadających profesjonalne oprogramowanie wspierające zarządzanie podejmuje decyzję o jego wymianie. Dlaczego? Wszystko wskazuje na to, że przedsiębiorstwa zaczynają dostrzegać, że dotychczasowe systemy przestały być wydajne i nie są już w stanie zwiększyć ich mocy produkcyjnych oraz zrobić kolejnego kroku na drodze do Przemysłu 4.0.
Trwająca na rynku wymiana systemów to nie chwilowy trend, ale konieczność, która zadecyduje o przewadze konkurencyjnej. Wiele z wykorzystywanych w polskich przedsiębiorstwach systemów ERP ma bardzo ograniczone funkcjonalności, ponieważ firmy wdrażały je kilka czy nawet kilkanaście lat temu w zupełnie innej sytuacji biznesowej. Przez ten czas przedsiębiorstwa zwykle bardzo się rozwinęły i potrzebują wsparcia ze strony IT na zupełnie innym poziomie.
Cel optymalizacja!
Jednym z silniejszych argumentów przemawiających za inwestycją w nowe systemy ERP jest dążenie do optymalizacji kosztów, co szczególnie widać w firmach produkcyjnych. Doświadczenia pokazują, że w przypadku przedsiębiorstw przemysłowych systemy klasy ERP i MES przyczyniają się do zwiększenia efektywności produkcji o 15-25%, zredukowania czasu przestoju maszyn o 30-50%, czy też skrócenia czasu wprowadzenia nowego produktu na rynek o 20-50%. Osiągnięcie podobnych wartości jest niemożliwe bez zastosowania inteligentnych algorytmów, które są w stanie zbierać dane z poziomu hali produkcyjnej, wykrywać i rozwiązywać niedostrzegalne dotąd problemy, związane choćby ze zużyciem maszyn, zmęczeniem komponentów czy optymalizacją wykorzystania zasobów wytwórczych.
– Współczesne systemy są znacznie bardziej funkcjonalne, łączą możliwości systemów ERP oraz BI, MES, HCM czy WMS. Są też znacznie łatwiejsze w obsłudze i mają nieporównywalnie większe możliwości analizowania informacji, co przekłada się na szybsze podejmowanie trafnych decyzji – zauważa Andrzej Morawski, wiceprezes zarządu firmy BPSC, dostawcy systemów wspierających zarządzanie przedsiębiorstwem. – Warto również wspomnieć o znaczeniu unijnych funduszy. Choć wsparcie jest niższe niż w poprzedniej perspektywie, to wciąż można dzięki pozyskanym środkom realizować znaczące projekty informatyczne. To dla firm dodatkowy bodziec, który skłania je do informatyzacji – dodaje Andrzej Morawski.
W takich momentach często pojawia się również pytanie i wątpliwość, czy aby nie lepiej wprowadzić modyfikacje. Jednak patrząc pod kątem optymalizacji kosztów modyfikacja starego systemu na dłuższą metę jest nieopłacalna i nieracjonalna. To trochę tak, jakby do starego samochodu zamontować spojler – choć wydamy pieniądze, to w praktyce zmieni się niewiele.
Utrzymywanie i modyfikacja starego systemu wymaga z jednej strony technologii integracyjnych, z drugiej czasu, zasobów osobowych i prowadzenia prac programistycznych. W sytuacji, gdy na rynku IT mamy do czynienia z dużą rotacją na rynku pracy, odejście z firmy członków zespołu odpowiedzialnego za modyfikacje oznacza ryzyko braku właściwego wsparcia systemu i perspektywę kolejnych wydatków. – Doświadczenie pokazuje, że nowy system bywa znacząco tańszy i łatwiejszy w utrzymaniu od starego, a przy tym jest nieporównywalnie lepszy od strony funkcjonalnej czy interfejsu użytkownika – przekonuje Andrzej Morawski z BPSC.
Wymiana to nie trend tylko konieczność
Analizując dane GUS-u można zauważyć, że w ubiegłym roku na rynku ERP rozpoczął się proces wymiany systemów i będzie on kontynuowany. Ze statystyk firmy BPSC wynika, że już co trzeci prowadzony proces przedsprzedażowy systemu Impuls EVO dotyczy wymiany dotychczas stosowanej aplikacji wspierającej zarządzanie firmą. Dla porównania, jeszcze 5 lat temu wymiana następowała w zaledwie 5% przypadków. Dane BPSC potwierdzają jednak ogólne rynkowe trendy. Według raportu Panorama Consulting Group niemal 17% wdrożeń ERP na świecie to właśnie wymiany. Oznacza to, że oczekiwania biznesu względem informatycznego wsparcia dynamicznie się zmieniają.
– Dobrym przykładem „pokoleniowej wymiany ERP” może być choćby jeden z naszych klientów, lubelska firma GT85 – producent myjni przemysłowych oraz maszyn dla przemysłu. To przykład przedsiębiorstwa, które zdecydowało się na wymianę systemu klasy ERP właśnie ze względu na szybki rozwój biznesu i niewystarczającą funkcjonalność wykorzystywanego do tej pory oprogramowania – wyjaśnia wiceprezes BPSC.
Firma wyróżniona w ostatnim czasie m.in. przez miesięcznik Forbes oraz Puls Biznesu, to założone w 1999 roku przedsiębiorstwo, będące na początku przedstawicielstwem angielskiej firmy produkującej smary, w 2007 roku zmieniło profil swojej działalności tworząc pierwsze myjnie ultradźwiękowe. Następnie dwukrotnie – w 2011 roku oraz 2014 roku – modernizowało i rozbudowywało park maszynowy. Zaczęło rozwijać się na tyle szybko, że wymiana systemu stała się nieodzowna. Mimo że GT85 do niedawna z powodzeniem używała systemu ERP we wszystkich obszarach przedsiębiorstwa, rozwój działalności w kierunku produkcji urządzeń myjących pociągnął za sobą konieczność wykorzystania znacznie bardziej wyspecjalizowanego rozwiązania wspierającego produkcję.
– Firma zdecydowała się więc na wdrożenie systemu Impuls EVO, a zakres projektu obejmował implementację modułów: CRM, gospodarka materiałowa, finanse i księgowość, kadry i płace, zarządzanie produkcją oraz dystrybucję – wylicza Andrzej Morawski. W związku z chęcią poprawy zarządzania samą produkcją, firma zdecydowała się również na wdrożenie MOM, czyli Mobilnego Obrotu Magazynowego, Elektronicznej Rejestracji Procesu Produkcji oraz Raportu PZM, narzędzia sprawdzającego się w bilansowaniu potrzeb przedsiębiorstw, których technologia produkcji zawiera sporą ilość półwyrobów, tak jak w przypadku GT85 Polska.
Co udało się osiągnąć? Stały dostęp online do każdego materiału wykorzystywanego w procesie produkcyjnym. Możliwa stała się kontrola minimalnych stanów magazynowych produkcji i stworzenie wirtualnego magazynu przyprodukcyjnego, gwarantującego łatwy dostęp do materiałów i półfabrykatów na stanowiskach produkcyjnych. A tym samym większa produktywność, optymalizacja zasobów i brak przekłamań i błędów, które powstawały wskutek ręcznego monitorowania danych.
Układanka ERP powinna być kompletna
Przed podobnymi wyzwaniami stają również inne przedsiębiorstwa, które szybko się rozwijają i w pewnym momencie stają przed koniecznością wymiany systemu, bo ten nie przekazuje np. informacji o całościowych kosztach produkcji lub nie pozwala skutecznie zarządzać zasobami ludzkimi. Badania, które przeprowadziła firma BPSC wśród swoich klientów w ubiegłym roku mówią, że choć 67% firm produkcyjnych posiada system ERP, to 47% z nich ma ograniczoną funkcjonalność.
– Z naszych doświadczeń wynika, że odsetek firm pozbawionych dostępu do bardziej zaawansowanych narzędzi planowania produkcji MPS (Master Production Scheduling), MRP (Material Requirements Planning) czy APS (Advanced Planning System) – jest jeszcze większy. Im dalej w informatyczny las, tym ciemniej. Szczególnie kiepsko wygląda sytuacja w przypadku rozwiązań klasy MES, które zbierają informacje online bezpośrednio ze stanowisk produkcyjnych i transferują je do obszaru biznesowego. Rozmawiamy z wieloma firmami, które dopiero teraz zaczynają poważnie myśleć o informatyzacji tych obszarów – wyjaśnia Andrzej Morawski, wiceprezes BPSC.
Trudno rozpatrywać np. zarządzanie technologią produkcji w oderwaniu od jej planowania, rejestracji, kalkulacji kosztów, kontroli jakości czy zarządzania wydaniami oraz przyjęciami produktów. System ERP powinien więc być postrzegany jako pewnego rodzaju układanka pasujących do siebie puzzli – jeśli jeden z elementów do niej nie pasuje lub też koszty jego integracji są nieracjonalne, to jest to sygnał, że wymiana jest konieczna. Teoretycznie wszystko da się zintegrować, pozostaje jednak pytanie o sensowność podjęcia takiej decyzji. W pewnym momencie nakłady przewyższają bowiem korzyści wynikające z połączenia aplikacji.
ERP dla wszystkich
Kiedyś systemy były dedykowane przede wszystkim szefom produkcji, finansów czy logistyki, dziś są narzędziem dostosowanym do potrzeb i wymagań niemal wszystkich pracowników w przedsiębiorstwie. Z jednej strony systemy ERP mają dostarczyć wiarygodnych, zintegrowanych informacji zarówno z wewnątrz organizacji, jak i źródeł zewnętrznych, ułatwiając tym samym podjęcie decyzji na wysokim szczeblu zarządzania, z drugiej współczesny ERP to narzędzie dla pracownika ułatwiające mu wykonywanie codziennych obowiązków służbowych. Przekłada się to na znacznie większą intuicyjność obsługi w porównaniu ze starszymi rozwiązaniami, możliwość mobilnego dostępu informacji czy bardzo rozbudowaną funkcjonalność, znacznie wykraczającą poza obszar, który zwykle utożsamia się z ERP.